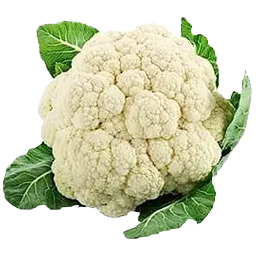
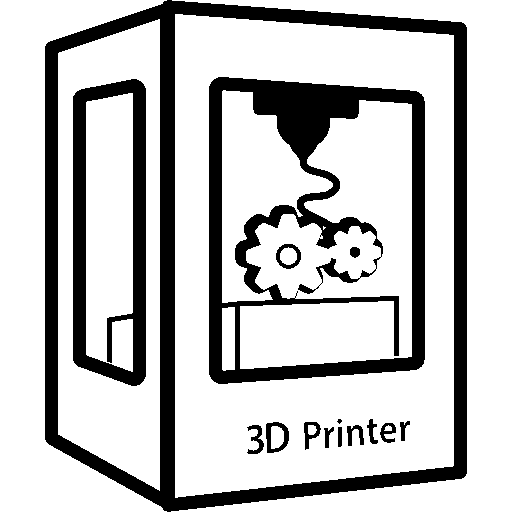
I wasn’t aware. I’ll look into this tomorrow. Thanks!
I wasn’t aware. I’ll look into this tomorrow. Thanks!
It’s not clogged: I fished out the mangled piece of TPU and printed something else with it straightaway - several times. Not sure why it starts clicking like that with that filament. Worse: it seems to do it almost always at the same point in that print.
I applied some glue to the sheet and it didn’t increase the adhesion by much, but it increased it enough and the print went through okay:
However, now I have another problem: I tried to print another one with the same material and the head started to make clicking noises mid-print and stopped flowing 😢 I’m not sure what’s going on with this now. Maybe I need to raise the temperature or something.
What have you done to clean the bed?
I cleaned it with water and dish soap. There’s nothing like it for adhesion. Even IPA doesn’t quite get the same results.
Has the TPU been dried?
I left it in the dryer at 55C for 3 days. The internal hygrometer says 13%, I tried drying it hotter than that, but then it seems to have trouble travelling through the silicone tube - like friction or something.
What’s the max speed you’re printing at?
Whatever the default is for the Prusa-supplied preset for this very filament brand and make. I just lowered the nozzle temperature to prevent stringing and material “balling up” on the surface, and I raised the bed temperature to increase adhesion a bit.
In addition to a brim, have you tried adding supports?
There is a ton of support for that part: it’s organic support and it’s growing inside and outside the part without ever touching the part itself. The reason being, it’s basically a thin bellows that’s two layers thick, so I don’t want anything supporting the bellows, or any support growing from the bellows, because it’s super-fragile and it won’t survive removing the support. That’s one of the reasons why we ordered a Prusa XL with 2 heads: one will extrude the part in TPU while the other will extrude the support in PLA, which should fall right off.
So since I told the slicer to avoid touching the bellows with the support trees, there’s a lot of it going around it on the outside. And indeed the bits of parts that I managed to print so far seem quite stiff and nicely supported. But the problem is, the entire thing simply comes unstuck and flies off the bed when it becomes too heavy.
It’s heavy on both sides. Also, I need to keep this thin wall facing up because otherwise it would be essentially impossible to remove from the support. And I need the bits facing up to be very clean, while I can afford some nastiness on the bit that faces down after I’m done removing and cleaning the supports.
I added a giant brim all around the part (connected to the part). The whole thing - part, brim and all - simply comes unstuck.
Thanks.
I tried lowering the speed (I can’t see any settings to limit it in only one axis though) but from what I read is safest for TPU / TPE, it turns a 2-hour print into a 2-day affair. Not an option for a printer that’s used by everybody in the company all the time.
You were right: after some trial and error, I backed off both idler tensioning screws 2 full turns and then the print went without a hitch. It looks cleaner too. And I don’t know if it’s related (now sure how it would be, but who knows…) the part didn’t warp. First time I get a complete straight TPU part.
Thanks for the tip!